The list of possible machinery-related injuries is as long as it is horrifying, from crushed hands and severed fingers to blindness. There seem to be as many hazards created by moving machine parts as there are types of machines. Safeguards are essential for protecting workers from needless and preventable injuries. Here’s our answers to some of our clients’ most frequently asked machinery safety questions:
Why do most machine-related accidents occur?
Accidents usually result from a combination of factors that include both hazardous machine conditions and careless human actions. That’s why any machine part, function or process that may cause injury be safeguarded and that operators of machinery and others in the vicinity of machinery operations be trained to recognize hazards and safety operate their machines.
Which machinery mechanisms are most hazardous?
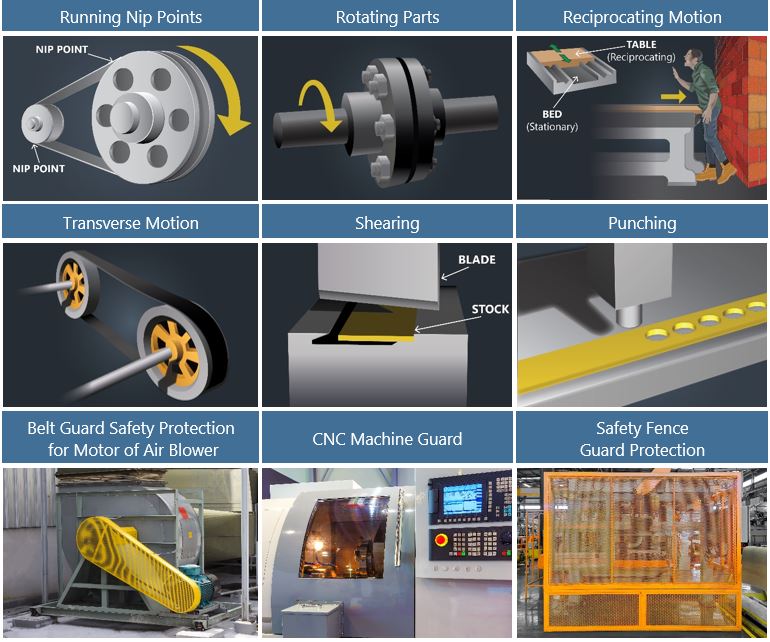
What is machine safeguarding?
- Prevent contact. Prevent any part of a worker’s body from contacting dangerous moving parts or ejected material.
- Secured & well-constructed. Workers should not be able to easily remove or tamper with or otherwise disable a safeguarding device.
- Protect from falling objects/contain the hazard. The safeguard should ensure that no objects can fall into moving parts.
- Create no new hazards. A safeguard defeats its own purpose if it creates a unintended hazard such as a shear point, a jagged edge, or an unfinished surface which can cause a laceration or create a pinch point.
- Create no interference. Any safeguard which impedes a worker from performing the job quickly and comfortably might soon be overridden or disregarded.
- Allow needed access. Safeguard systems should be constructed to allow convenient access for routine, repetitive tasks that are part of normal operation of the machine, such as part loading and unloading and maintenance, such as lubrication, without compromising safety.
Where can I find the machine guarding standards my company must comply with?
- American National Standards Institute (ANSI) B11 series
- National Fire Protection Association (NFPA) 79 Electrical Standard for Industrial Machinery
- International Organization for Standardization (ISO) – various standards covering all aspects of machine safety
Which of the standards does OSHA usually cite for violations?
There are two specific citations, OSHA’s catch-all for machine guarding, that they’re most likely to cite. Those are 29 CFR 1910.212(a)(1), which covers general requirements to provide machine guarding, and 29 CFR 1910.212(a)(3)(ii), which focuses on point of operation guarding. OSHA may also cite the General Duty Clause and reference other consensus standards mentioned above.
What types are safeguarding approaches are best?
Safeguarding machinery, whether through eliminating or controlling the hazards, is not a one-size-fits-all approach. Guarding may be required to restrict operator access to a mechanical hazard, contain ejected materials, or prevent chemical exposure.
A guard as defined by OSHA is an enclosure that prevents anyone from reaching over, under, around, or through, and offers the highest level of protection. Some different types of guarding are:
- Fixed – usually a permanent part of the machine that prevent access to the danger area.
- Interlocked – when this type of guard is opened or removed, the tripping mechanism and/or power automatically shut off or disengages, and the machine cannot cycle or be started.
- Adjustable/Self-Adjusting – the openings of these barriers are determined by the movement of the stock.
- Access Control Devices – There are several means of electronic access control, including presence sensing devices such as light curtains, area laser scanners, or pressure mats which allow operator access to the machine, but will prevent the actuation of the hazardous motion, when a person or body part is in the hazard zone. Two-hand controls require concurrent, sustained hand actuation, to keep the operator(s) hands out of the point of operation during the hazardous motion of the machine. Adjustable or moveable barriers such ass access doors or adjustable guards, that are provided with a safety rated interlocks require the guards to be in position before the hazardous machine motion initiates. These devices must be installed with dedicated safety circuits, where all components of the circuit are safety rated (i.e. control reliable).
The Machine Guarding Process
During the design of a new machine or modification of an existing machine, conduct a risk assessment to identify the specific hazards associated with the machine and the work being conducted, quantify risk and identify the appropriate safeguarding to reduce risk to lowest possible level, using the hierarchy of control. The risk is reassessed with the controls and residual risk determined. If the level of risk is acceptable, validate the effectiveness of the controls and document the process. This is shown graphically in the ANSI B11.0 Risk assessment process flow diagram below.
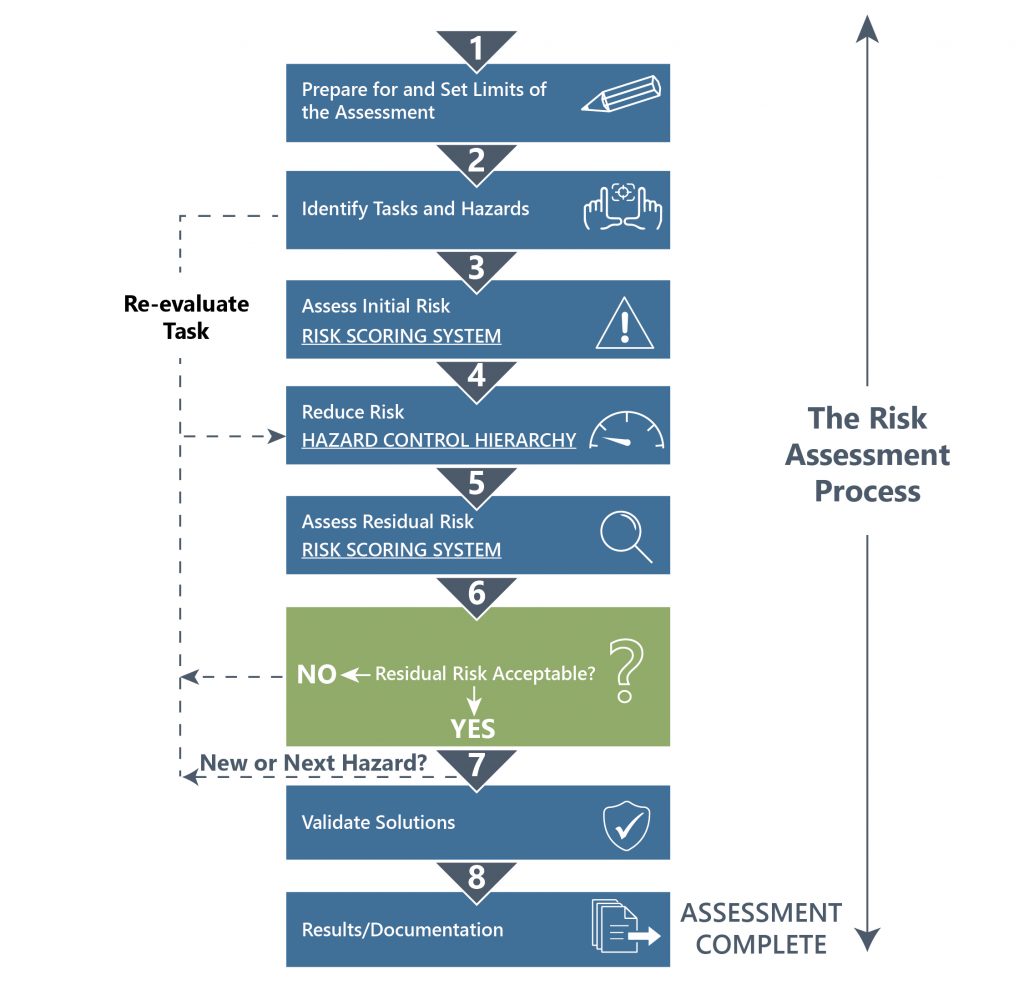
What else does safeguarding include?
There is more to machine safeguarding than just guarding machines. Even the most elaborate safeguarding system cannot offer effective protection unless the workers are also trained and competent to operate their machines This includes understanding the hazards of the process and the safety controls put in place. Operators should also periodically inspect their machines to verify that guarding is present and functioning properly. Maintenance employees must be similarly trained, and Preventive Maintenance processes should include verifying presence, condition and proper function of machine guarding systems. As with all safety systems, a periodic audit of the effectiveness of the overall machine safety program If you would like assistance implementing a comprehensive machine guarding program, contact us.