-
What’s the best way to have peace of mind that your facility is protected against an unplanned release of chemicals that could trigger an environmental, personnel or business catastrophe? We have four suggestions.
Our suggestions are based on the Occupational Safety and Health Administration (OSHA) process safety management (PSM) standard, which outlines fourteen interrelated elements of a regulated PSM program (shown below). Even if your facility does not handle a highly hazardous substance listed in OSHA PSM standard (29 CFR 1910.119), implementing these four key PSM elements can protect your facility against catastrophic release related to any chemical handling.
1. Gather process safety information (PSI).
PSI is the gathering of the physical and chemical properties of process chemicals, including maximum intended inventories, process operating limits, process safety devices, and relief calculations. Just gathering and understanding the PSI is a great first-step in ensuring that your chemical process is understood, designed, and operated in a safe manner. Even though a PSI is just one of the 14 elements, it can sometimes contain more information than the other elements, combined.
2. Conduct a process hazard analysis (PHA).
PHA is a semi-quantitative assessment of hazards and risks of the process under normal and abnormal conditions. A good PHA will be performed by various company departments involved in managing the process. Those departments typically include operations, engineering, maintenance, facilities management, and environmental safety and health. Working as a team, this group will break down the process into sub-sets or nodes and then analyze each node for potential deviations that could occur and the consequences of those deviations – thereby performing a risk assessment on each deviation. In a typical PHA, quantitative risk scales are used to rank the hazards and risks of each deviation so that recommendations made to further reduce risk can be properly prioritized. For a process that is subject to the OSHA PSM standard, a PHA is required every five years and must be retained for the life of the process. Even if a chemical process is not regulated by the OSHA PSM standard, it is a good idea for a facility to perform a PHA to assess the risks of a catastrophic chemical release event.
3. Implement a management of change (MOC) process.
As a facility gains experience with its chemical processes, inevitably, there will be changes made to the process to correct issues and optimize the process performance. Even changes made with the best intentions can have unforeseen consequences, which is why a MOC process is so important. A MOC process is a change approval process that engages the departments associated with a process so that they can weigh in on the aspects of the intended change. In this way, changes made to the process are evaluated by the affected departments who can then approve or modify the change. The goal of the MOC is to ensure that changes do not increase the risk of a process deviation and that unintended consequences are addressed prior to the implementation of the change.
4. Analyze safeguards with a layers of protection analysis (LOPA).
Though not an element of the OSHA PSM regulation, performing a LOPA is also beneficial to a PSM program. Many facilities rely heavily on the training of its operators and the soundness of its standard operating procedures to minimize the risk of deviations. In many cases, these are the only controls for older chemical processes designed and built prior to the introduction of process control technology and programmable logic controllers (PLC). If, during the PHA, the facility finds that there is a reliance on one or two key engineering, administrative or personal protective equipment interventions to safeguard the process, then a LOPA may be beneficial. A LOPA will help further analyze and validate some of the semi-quantitative judgments made during the PHA by looking at failure rates of specific safeguards. A LOPA is a great way to help determine and justify the need for engineering controls over administrative and personal protection solutions.
As with exposure to any hazard, employers should consider the hierarchy of controls from the National Institute for Occupational Safety and Health:
Eliminating a hazard is the most effective method for controlling process risk. The use of personal protective equipment (PPE) is considered the least effective method of controlling exposures to a hazard. The use of interlocks and automated process controls would be considered an engineering control. Standard operating procedures and employee training would be considered administrative controls.
Here’s an overview of our four suggestions:
- PSI - Collect and understand the chemical and physical properties of the chemicals in the process. Understand how safety systems work and what triggers them in the event of a process deviation.
- PHA – Perform a PHA that assesses the severity and likelihood of process deviations so that risks can be prioritized and managed effectively.
- MOC – Develop and implement a MOC process to ensure process changes are understood by process owners and do not result in unintended consequences.
- LOPA – Consider performing a LOPA to determine the effectiveness of safeguards that are present in the process and validate the semi-quantitative risk assessments in the PHA.
Implementing these key elements for process safety management can help employers reduce the risk of a catastrophic event and bring peace of mind to the idea that it won’t happen to us. If you would like more information about how to optimize your process safety management system, please contact us.
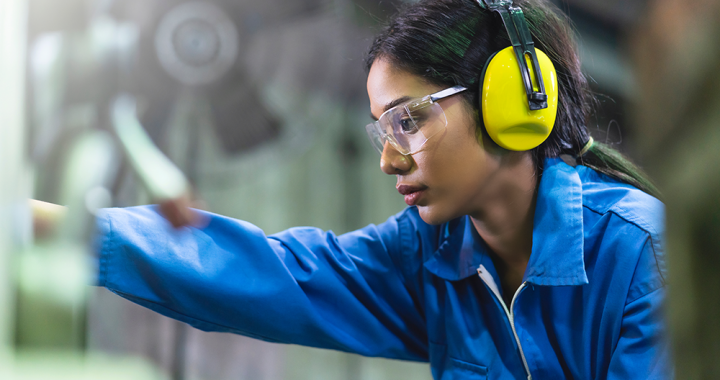
Process Safety Management 101: 4 Must-Dos to Protect Against Catastrophic Release
Posted in Insights/Innovation.