-
Ergonomics = the science of designing the job for the worker, rather than forcing the working to fit the job.
With so many back-to-work concerns in the midst of the COVID-19 pandemic, creating and implementing an ergonomics improvement process can feel rather low priority.
In fact, the emotional toll of the COVID-19 pandemic, which is causing increased fear, fatigue and frustration, is a great reason to do what you can to eliminate the “low hanging fruit” of fatigue and frustration that accompanies suboptimal workplace design.
Whether evaluating newly functioning remote workspaces or those workspaces that are recently reopening businesses, an ergonomics improvement process can:
- Enhance productivity and worker wellness, which contributes to your company’s bottom line
- Reduce costs associated with compromised worker health and musculoskeletal disorders (MSDs), which account for over 30% of all worker injury and illness cases (Bureau of Labor Statistics)
- Create efficient workplace layouts that consider work methods, machine interface, and the work environment
- Remove barriers to maximum safe work performance and accommodate for workers’ physical and psychological capabilities
To get the most reliable ergonomics analysis possible, we have three recommendations:
1. Engage a third-party certified health and safety expert, someone who can evaluate your workspace processes and designs with objective “fresh eyes.”
Fresh eyes can notice the strains, repetitive motions, awkward postures, vibrations, lighting and pressure points – those factors that increase ergonomic risks – that can oftentimes go unnoticed.
2. Insist on an assessor who is well-versed across a multitude of industries.
The broader the industry experience of the assessor, the better they’re able to draw from and apply cost-effective, innovative lessons learned and best practices from various industries.
3. Make sure your assessor actively involves the worker, as well as onsite environmental, health, and safety (EHS) staff.
Employees, when conscientiously solicited, can offer a wealth of insight for not only identifying problems but also envisioning practical solutions. Collaborating with employees uncovers essential lagging indicators (such as injury frequency/severity, lost workdays, worker’s compensation costs) as well as leading indicators (such as employee surveys and ergonomics training) for a more comprehensive assessment.
4. Focus on problem resolution, not just problem-finding.
The goal of an ergonomics assessment is not to compile a list of risk indicators, but to create a companion tracking tool that quantifies ergonomic risk and recommends process improvements for immediate risk reduction and long-term process engineering.
Want help with cutting costs and improving productivity at your facilities?
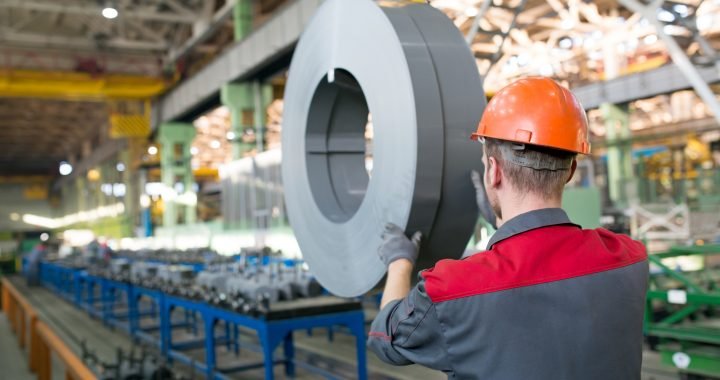
Cutting Costs and Improving Productivity with Ergonomics
Posted in Insights/Innovation.